I love a wood burning fire. I love the look, the smell and the soul warming heat. But, we don’t always have room for a wood burning stove. Sometimes we’re in a small nylon tent, a small sailboat or even a snow cave. When these situations arise, what do you use for heat?
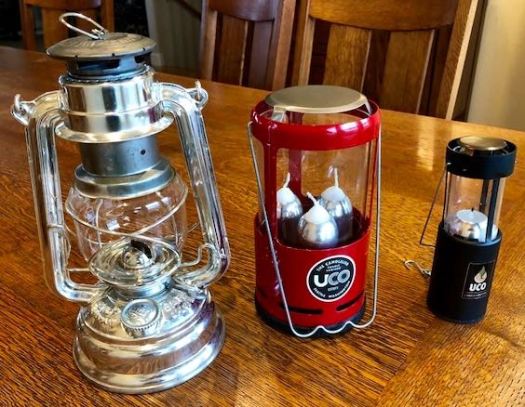
I love all 3 of the above items for slightly different reasons. Let’s discuss the good, the bad and the ugly:
Let’s start by describing both ends of the spectrum:
First Up: The Feuerhand Baby Special #276.
This is the official Scamp logo lantern. I bought 4 of these lanterns before I even knew anything about the Scamp sailboat. But, destiny was alive and well, for when I discovered the small sailboat using this exact same lantern that I had grown to love for their logo, I knew something special was about to happen.
The Good: They’re high quality built in Germany lanterns. They burn a long time. Like, I’m not sure how long, but a long time. They’re very wind resistant. They get wider at the base for increased stability. There a joy to use and set next to you during the evening to unwind.
The Bad: Not really bad, but rather a limitation of any liquid fueled lantern, if the lantern is left on it’s side, the oil will spill out. This isn’t a problem on your deck or nightstand, but it is on your sailboat. I use this lantern around the house for mood lighting and for power outages.
Next Up: The UCO Candle Lantern:
This single candle lantern has worked well for me in a small 2 man backpacking tent. It’s light weight and diminutive size make packing a breeze. It brings ambience into an otherwise cool and dark tent, lightening spirits and providing a noticeable degree of warmth.
The Good: Lightweight, small, burns for 9 hours on a single candle. Easy to light with the retractable glass mantle.
The Bad: Limited light and heat output. Enough for a small backpacking tent but not much more.
Up Next: The UCO Candlelier:
I’ve been brooding over this purchase for some time, but finally decided to pull the trigger. This 3 candle design from UCO might just well be the ticket for your 3 man tent and or your Scamp sailboat. During a fall overnighter on Shackleton (Scamp sailboat), I took the single burner UCO Candle Lantern and a Mr. Buddy Heater. The single candle wasn’t enough heat, and the Mr. Buddy Heater was way too much heat. The literature for the UCO Candlelier states it gives off a whopping 5,000 BTU, plus now I have 3 distinct heat settings.
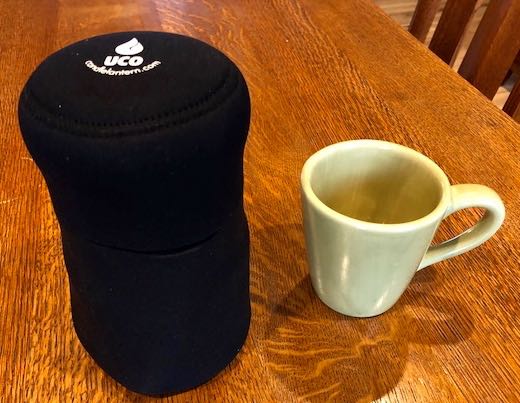
The neoprene cocoon protects the lantern during transport. This lantern is about the size of a 1 liter nalgene bottle.
Advantages of paraffin wax as a heat source when voyaging:
- Paraffin won’t spill out of the lantern.
- Paraffin won’t leak from it’s storage container.
- Paraffin stores and transports easily without any special considerations.
- Paraffin is virtually odor free.
- Paraffin UCO candles last 9 hours.
- The 3 candle lantern allows three different heat settings: High, medium and low.
I just received my UCO Candlelier today via UPS. I have high hopes that this larger, 3 burner candle lantern will be just the ticket for Hagoth, my Skiff America and my Hilleberg Nammatj 3 man tent. Based on my experience with the single candle lantern, I think I’m going to love this larger, hotter design.